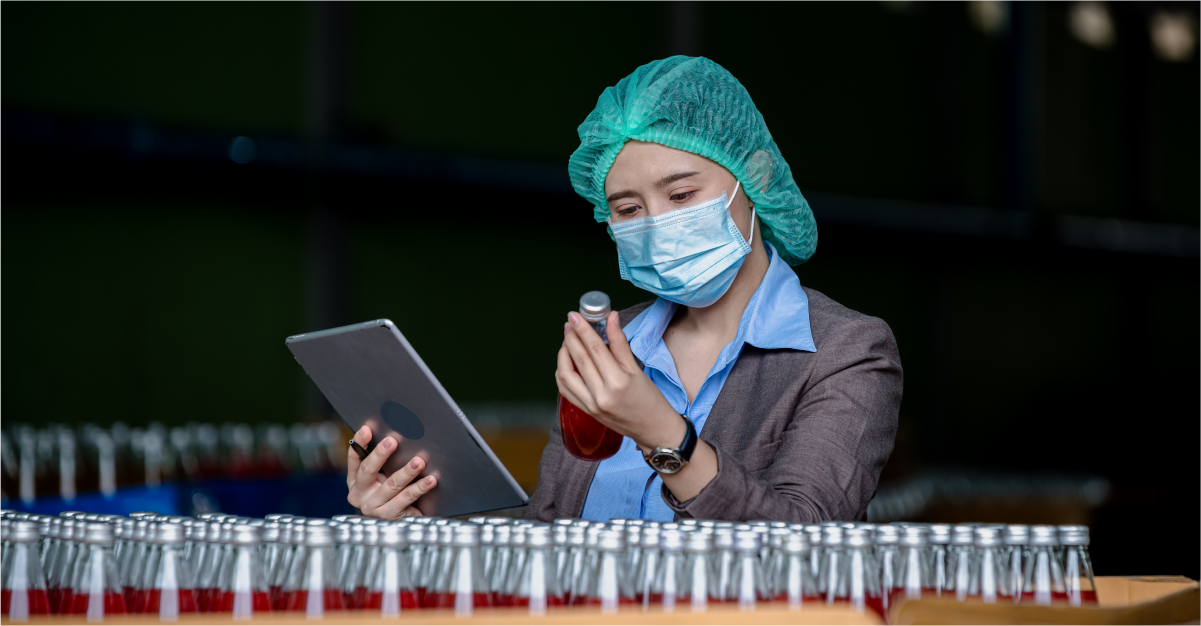
How 4Industry Drives Continuous Improvement and a Better Operator Experience
Before this company’s world-famous soda makes it to your table, it’s traveled a long journey through factory machines and hundreds of people who oversee its path from raw ingredients to a perfectly crafted, crisp cold beverage.
Operating over 130 factories in more than 70 countries around the globe makes it a significant challenge to maintain consitently qualitative end-products. Therefore, the company made it a priority to drive continuous improvement on a global scale.
Company size
80,000+
Industry
Food and Beverage
Number of plants
130+
Modules
Deviation Management | Root Cause Analysis | Smart Forms
-20%
in engineer travel time.
-20
days in mean time to resolve for defects.
70%
Built on ServiceNow, the 4Industry app has near-perfect uptime of 99%.
130+
of this company’s factories already use 4Industry.
Finding a way to monitor, log, and correct production issues was a top priority to reduce, costs, increase OEE, and improve operator satisfaction. They wanted a solution that empowered their engineers and operators with a means to access and share information in real-time – and via mobile – to perform their jobs more efficiently.
4Industry, an app built on ServiceNow, was specifically designed for this purpose. Completely customizable to meet each plant’s unique needs, the app allows the company’s operators and engineers to manage incidents and changes. Using digital Task Management to perform and schedule jobs combined with the machine learning engine of ServiceNow to suggest solutions, 4Industry brought both a proactive and predictive approach to maintenance in the breweries.
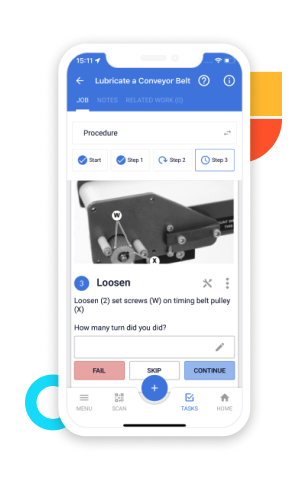
Creating easy access to information
Using the app, workers can access relevant information (OPLs, photos, step-by-step instructions, drawings or designs and Q&A functionality to name a few) needed to perform their job swiftly when working on a change or incident.
Monitoring audits, follow-up tasks, and CAPAs
Equally important, the app enables workers to log, upload and share information about what they see in the brewery and discover in the process of work, facilitating a fast exchange of information between team members and/or operators and management. This information is crucial for both continuous improvement and training efforts.
Since connectivity in production facilities is often lacking, the app isn’t reliant on a connection to the Now platform, and is designed to function on its own.
Providing data to assess performance and opportunities
Because the platform aggregates data from all app users, it sits on an enormous amount of valuable information that can be used to avoid downtime and cut overhead costs. For example, when a bottling machine runs into an issue, the engineer responsible for that machine is provided with the possible causes and solutions for the incident based on historical data. If this particular incident occurs regularly, root cause analysis is executed within the app so a permanent solution can be designed.

Information collected by 4Industry is displayed in digital dashboards that provide actionable insights so management spends less time filling out spreadsheets, and more time analyzing data to improve operational performance.
Benefits
- Faster way to monitor, log, and correct production issues
- Real-time information sharing between engineers and operators
- Instant access to OPLs, photos, and step-by-step instructions on mobile
- Continuous uptime of the application, even without internet connection
- Auto-suggested solutions based on historical data
Related Articles
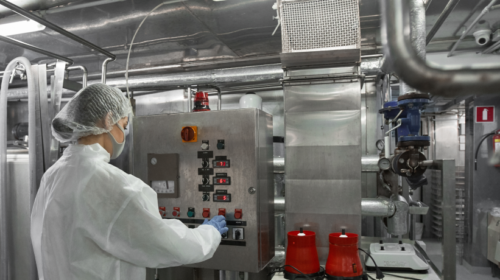
How 4Industry Automated a Global Coffee Company’s Audits
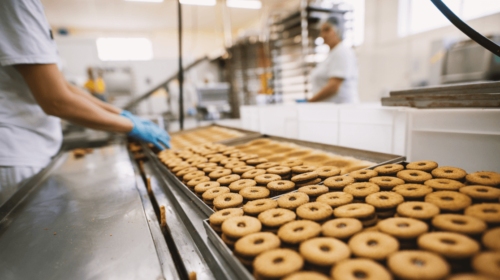