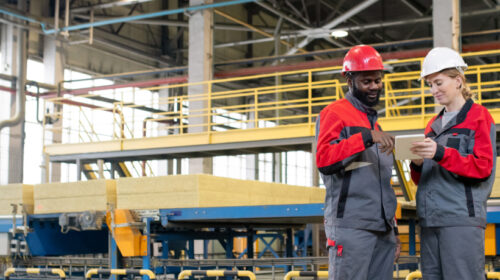
All You Need to Know About Heijunka in Manufacturing
Read our complete guide to heijunka in manufacturing, including a definition, examples, tips, and a heijunka box template.
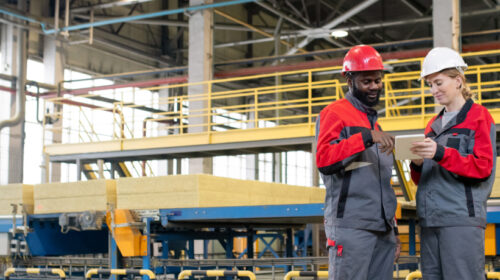
What is Heijunka in Lean manufacturing?
Heijunka is a fundamental concept in Lean production that helps manufacturers balance and level variation within a production process.
Sudden spikes in demand can lead to enormous pressure on the shop floor, burdening both equipment and operators. Additionally, most factories produce multiple products, resulting in a variability of process times and product volume.
Heijunka addresses these problems by averaging production volume over a specific time span and efficiently ordering the production of multiple products.
In this post, we will explore everything you need to know about Heijunka. Let’s begin by looking at the benefits of Heijunka compared to classical batch production.
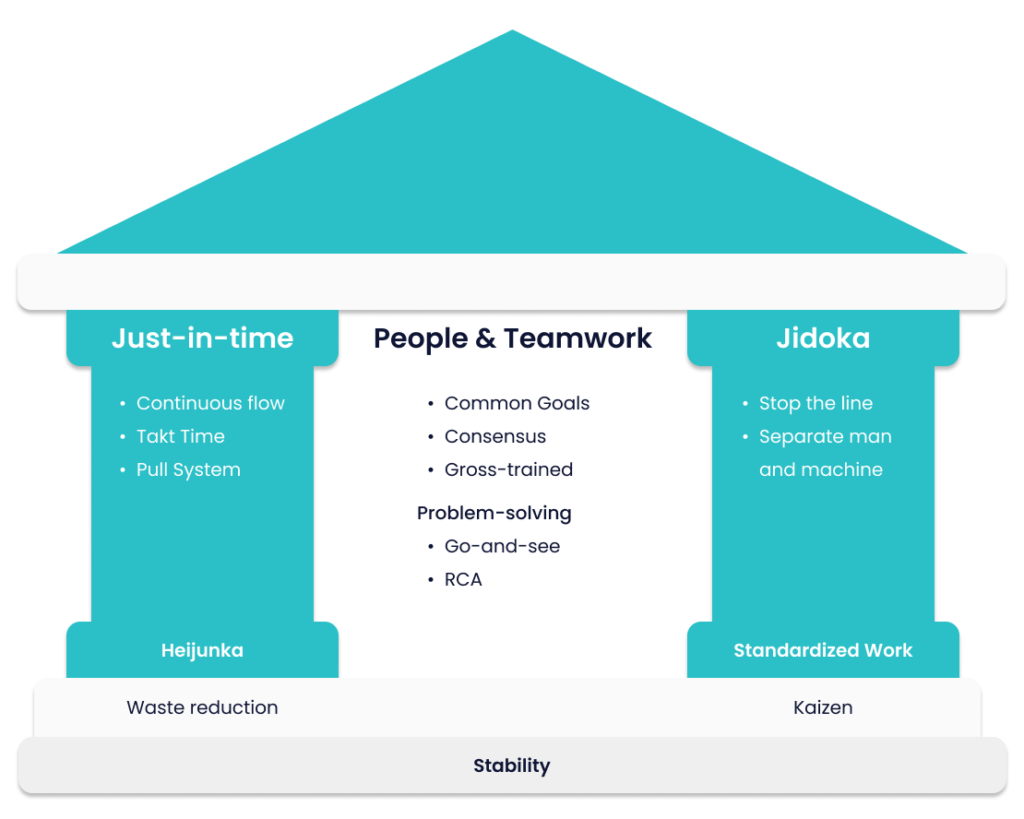
What are the benefits of Heijunka?
Like many concepts in Lean manufacturing, Heijunka originates from the Toyota Production System (TPM).
In classical Fordian production, products were mass-produced in large batches.
At a certain point in time, Toyota concluded that batch production was an inefficient way of meeting customer demand. This realization was due to the fact that batch production inevitably led to waste (Muda) and overburdening (Muri). And that, naturally, led to lessened profits, unhappy workers, and degrading machines.
Heijunka, on the other hand, spreads the expected number of orders over multiple days. This is known as “levelling by volume” and entails producing the same number of products every day, thereby preventing sudden spikes in demand from overburdening the shop floor.
In contrast to batch production, a Heijunka system enables manufacturers to produce with a minimal inventory and lower lead time. Additionally, Heijunka production is more predictable and stable, and therefore adaptable to shifts in demand in a way that doesn’t cause excess inventory or waste.

The two aspects of Heijunka (with examples)
Leveling by Volume
As mentioned earlier, levelling by volume involves spreading the average order volume over a week. Here’s a quick example:
A furniture company receives an average of 700 orders a week for a specific desk chair. However, the exact number per day, varies: 150 on Monday, 75 on Tuesday, 90 on Wednesday, and so on.
By implementing Heijunka, the company would produce 100 chairs every day. This approach ensures stable and predictable production, preventing both machines and workers from being overwhelmed by sudden spikes in orders.
Leveling by Type
When a factory produces multiple products, “Leveling by Type” can be a useful tool to streamline production. Instead of producing a large quantity of a specific product at once, different products are grouped together, ordered in a specific sequence, and produced in small batches.
For example, let’s say that a shoe company produces three sorts of footwear: sneakers, boots, and loafers. In classic production, they would produce a large batch of sneakers on day 1, a batch of boots on day 2, and a batch of loafers on day 3.
However, with Heijunka, a smaller quantity of each type is produced every day. For instance, they might produce 300 sneakers, then 100 boots, then 50 loafers.
What is a Heijunka box?
A Heijunka box is a tool that helps visualize the daily workload required to meet expected demand.
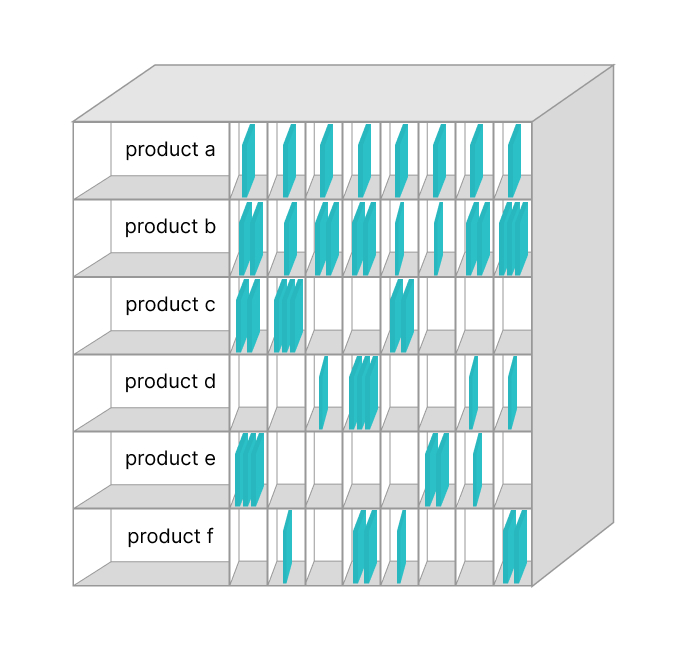
Essentially, the Heijunka box visualizes these three things:
- The type of product that must be made (displayed as a vertical row to the left)
- The number of batches of that product that must be made in a day (indicated by the number of cards in a compartment)
- The order in which different products need to be made (represented by vertical rows going from top to bottom).
As you can see, the vertical rows order the variety of products that must be made during daily production, while the horizontal rows how many batches of a specific product must be made on a given day of the week.
How to create a Heijunka box (with template)
Heijunka boxes can be created in various ways: physical cabinets with cards, drawings on paper or a whiteboard, or dedicated Connected Worker software like 4Industry.
If you want to start using Heijunka, you can use the template below. Just fill in the outer left row from top to bottom with the products you make and fill each compartment according to the number of required batches. It’s as easy as that!
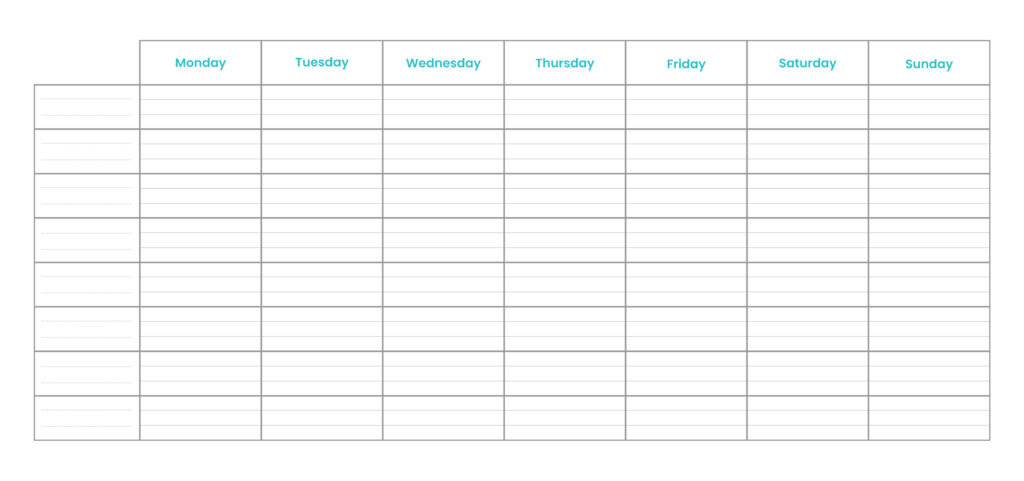
How to implement Heijunka in manufacturing
Let’s explore how you can implement Heijunka in manufacturing in 4 steps.
1. Group your products
First, you need to index all of your products and group them based on similarities. This enables you to create an optimal schedule and therefore an efficient production process.
2. Level production over time
This is where levelling by volume comes in. Average out your expected demand and divide that over your available production days. For this step, you need to keep your production capacity in mind; takt time, therefore, is a key concept.
3. Create a schedule
Now that your products are grouped and your production is levelled, you can combine the two in a Heijunka box. Once that’s done, you can proudly say that you’ve Heijunka-fied your production! However, to ensure continuous success over time, there’s one additional step.
4. Continuous Improvement
Once you’ve established your Heijunka system, you need to maintain a constant focus on opportunities for improvement and efficiency gains. This means monitoring demand and adjusting batch size accordingly, optimizing your Heijunka schedule, and identifying opportunities for continuous improvement on the shop floor itself.
Summary: the benefits of Heijunka
Summary: the benefits of Heijunka
In short, the benefits of Heijunka are:
- Reduced inventory due to smaller batches
- Lower lead time
- Increased adaptability to spikes in demand
- Stabler and more predictable production
- Less stress on machines and workers
- Reduced chance of overproducing

Frequently asked questions about Heijunka in manufacturing
What is the difference between Heijunka and Just-in-Time (JIT) manufacturing?
Heijunka and just-in-time manufacturing are both important concepts within Lean. They have one key thing in common: the aim to reduce waste and improve efficiency. However, their approach toward that goal differs in the following way.
Heijunka focuses on levelling production by averaging expected demand. It therefore relies on a forecasted volume, which adds an element of uncertainty to the method.
Just in time, on the other hand, produces only ordered items in the required quantity. This results in a smaller inventory but a much less predictable production schedule.
As you can see, each method has its pros and cons: with Heijunka, you end up with more inventory and a higher chance of overproduction. Just in time, in contrast, adds an element of unexpectedness and unpredictability to production.
How do you pronounce Heijunka?
Heijunka is a Japense word. Its most common pronunciation in English is hi-JUNE-kuh.
Table of Contents
- What is Heijunka in Lean manufacturing?
- What are the benefits of Heijunka?
- The two aspects of Heijunka (with examples)
- What is a Heijunka box?
- How to create a Heijunka box (with template)
- How to implement Heijunka in manufacturing
- Summary: the benefits of Heijunka
- Frequently asked questions about Heijunka in manufacturing
Related Articles
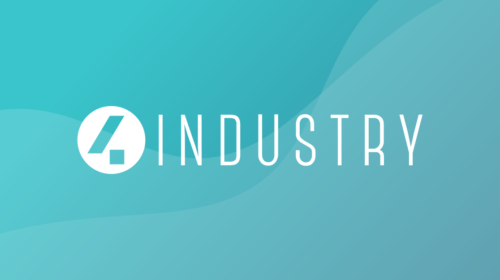
Manufacturing Glossary
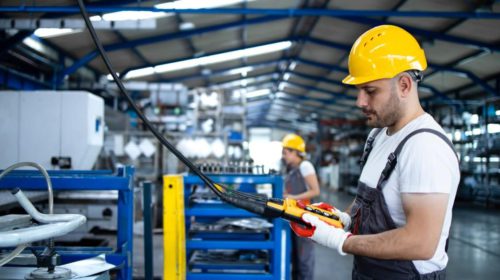